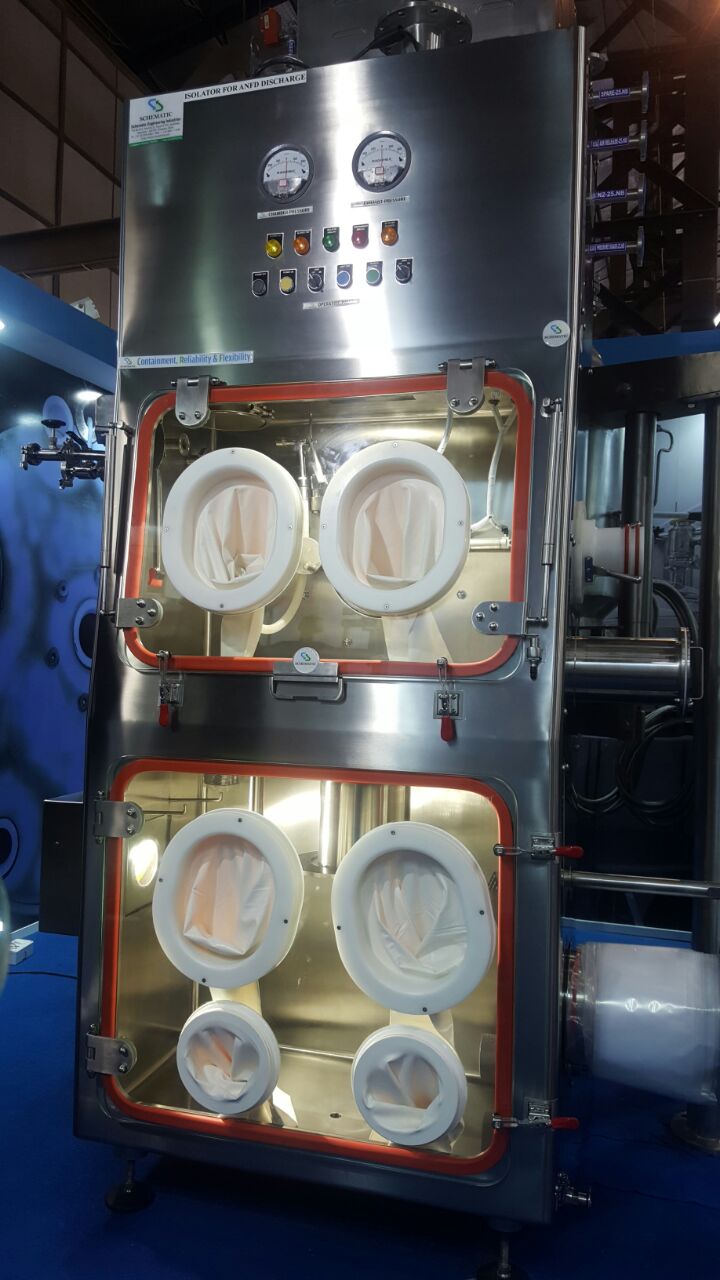
Agitated Nutsche filter Dryers (ANFD's) are widely used in the paint, pharmaceutical, chemical and R&D laboratory industries for the filtration and drying of active pharmaceutical ingredients (API) and chemical compounds. Plant managers understand that ANFD's offer a huge production efficiency benefits in that the filtration and dryer occurs in the same sealed unit, reducing media transfer losses and improving finished product quality.
During the ANFD filtration process, filtration occurs under vacuum or pressure in a closed vessel. After filtration, the processed media is dried into a cake substance. This operation has thus won favour by modern plant engineers as safety requirements and environmental concerns of solvent evaporation are addressed by the single unit.
A typical Standard Group ANFD consists of a dished vessel with a perforated filter plate/trolley which is typically mounted at the bottom of the vessel. The entire vessel is kept at the desired temperature by using a heating jacket, jacketed bottom dish and/or a stirrer (blade and shaft) through which heat transfer media can flow. Clearly, the vessel is made completely leak-proof for vacuum or pressurized service and typically complies to international pressure equipment directives/regulations.
During operation, the multipurpose Standard ANFD agitator performs a number of 3-axis operations with movement in axes both parallel and perpendicular to the shaft and importantly slurry contents can be kept fluidized until most of the mother liquor is filtered out. Repetitive washing, filtering and cake processing is conducted by a variety of reslurrying and vacuum techniques until the desired uniform cake consistency is created. This cake is then discharged by lowering the agitator and rotating it in such a manner that it brings the cake towards the vessel discharge port.
Unfortunately, all known ANFD designs to date suffer, to some degree, from residue cake left in the vessel and/or on the filter plate/assembly. After the ANFD paddles discharge the bulk of the cake through the discharge orifice, a small layer of cake (around 10-15mm thick) is left in on the filter, given the filter is positioned beneath the paddle, and is thus this cake is scrapped/wasted. For expensive pharmaceutical products this waste is very costly. Not only is this issue a commercial problem for the plant, it is invariably a quality issue as left over cake creates cross contamination risk/potential for the next batch, and a safety issue as operators are potentially exposed to dangerous substances.
The team at Schematic and its associated group of companies, has addressed these conventional ANFD problems by creating an innovative ANFD with an integral low-profile barrier isolator. The advantages and features are discussed below.
Schematics Agitated Nutsche filter Dryer (ANFD) offers significant plant advantages including;
Schematic Engineering Industries provide innovative integral Barrier Isolator technology for ANFD's which offer significant plant advantages including;