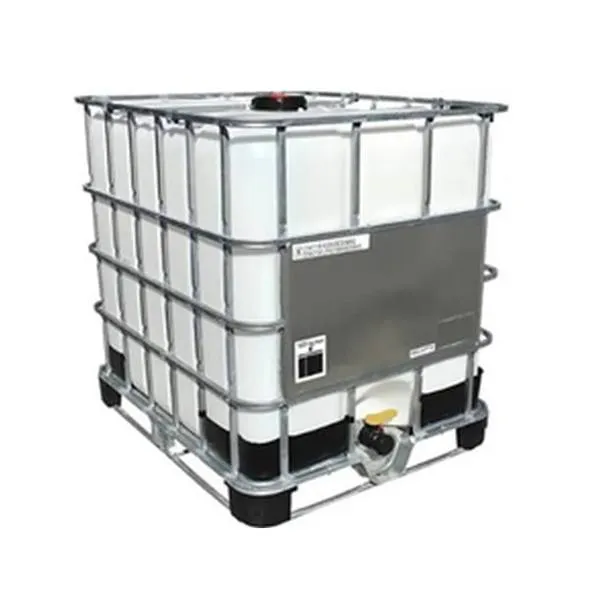
FOREWORD: Intermediate Bulk Containers (IBC’s) are used to store, handle and transport bulk materials, such as liquids, concentrates and purees from supplier/source to a client or processing plant.
There are many different types of IBC’s used for liquid handling including the ‘Metal framed ’IBC design, shown to the right.
This type of IBC has a hard plastic container, typically made from a blow-moulded plastic material such as HDPE (high-density polyethylene), which is enclosed by a galvanised metal frame. In today’s highly cost competitive and environmentally aware world, supply chains which employ this type of metal framed IBC are under severe pressure to change/upgrade them. The reasons for which are discussed below.
DISCUSSION: There are many problems and operational issues associated with metal framed IBCs with rigid ‘thick-walled’ plastic HDPE containers. Below are 10 of the common issues encountered:
[1] Stackability: Most metal framed IBC’s do not stack correctly. This is primarily down to the design of the metal frame and the poor location/seating surfaces on the top and bottom of the IBC.
Operators therefore use ‘work-arounds’ such as cardboard/wooden spacers in-between the stacked IBC’s, to help the IBC seating process (as shown). This practice introduces a significant stacking risk, as forklift operators can easily misalign the IBC’s and create a health and safety risk to plant operators and the contained produce inside the IBC. This risk to plant and person can be seen by the blue-arrows in the photo.
[2] Corrosion: Metal frames, if not properly protected or maintained, can be susceptible to corrosion. Exposure to moisture, chemicals, or harsh environmental conditions can cause rust and corrosion on the frame. Corrosion weakens the frame's structural integrity and can lead to safety hazards or even failure of the IBC
[3] Chemical compatibility: Plastic IBCs are designed to be compatible with a wide range of chemicals. However, the metal frame may not have the same chemical resistance properties. If the frame comes into contact with corrosive or reactive substances, it can lead to chemical reactions, degradation of the frame, or contamination of the stored contents.
[4] Physical damage: Metal frames can cause physical damage to plastic IBCs if not handled properly. Rough edges, sharp corners, or improper alignment of the frame can puncture or scrape the plastic walls, resulting in leaks, cracks, or structural weakness. Physical damage compromises the functionality and safety of the IBC.
[5] Heat transfer: Metal frames have higher thermal conductivity compared to plastic containers. This can lead to heat transfer from the frame to the stored contents or vice versa. In some cases, heat transfer can cause temperature fluctuations, potentially impacting the stability or quality of the contents. Inconsistent quality of ingredients is a big problem for a food and drinks processing plant as it can lead to lumps and random degradation of the final product.
[6] Cleaning challenges: Metal frames can pose challenges during the cleaning process. Corrosion, dirt, or debris accumulation in the frame's crevices or hard-to-reach areas can make thorough cleaning difficult. Inadequate cleaning may result in contamination risks or hygiene concerns.
[7] Weight and handling: Metal frames add weight and bulk to the overall IBC, making it heavier and potentially more challenging to handle, transport, or store. The additional weight can also affect load capacity and stability, requiring careful consideration during operations.
[8]Transport Costs: Metal framed IBC’s are not foldable. This means that return IBC transport costs (from client back to the supplier) are just as expensive when the IBC’s are EMPTY as the outward transport costs (supplier to client) when the IBC’s were FULL. These additional supply-chain costs ultimately impact on the cost of the final product, whether that is a can of cola or a tube of puree.
[9] Environmental Costs: In addition to the environmental impact of the vehicle fuel and emissions of returning empty “fixed framed” IBC’s on return transport, the large, thick-walled plastic blow-moulded containers are typically only used once. This is because the reality is that it is technically and commercially very difficult to clean the inside surfaces of the plastic IBC’s to the required food quality standards. This means that these IBC plastic containers are, in effect, a SINGLE USE PLASTIC (SUP) item which ultimately impacts on the processing factory/client’s environmental footprint.
[10] Replacement HDPE Container Costs: With thousands and thousands of plastic HDPE containers being used daily in a large food and drinks production processing plant, it will be obvious to the experienced reader that these costs can be significant when the item is only used ONCE.
Therefore, eliminating these costly thick-walled HDPE containers is a huge cost saving opportunity for the process plant/client and supply chain.
METAL FRAMED PLASTIC IBC UPGRADE OPPORTUNITIES
Given the huge opportunities for cost savings, health & safety benefits and environmental savings, many clients/processing plants and supply chains, across the world, have moved their operations to use foldable plastic IBC’s as shown below.
With folding ratios up to 4:1, foldable plastic IBC’s make huge sense for Return Transport, as they effectively utilise the waggon space. These foldable plastic IBC’s are therefore employed by clients for ALL bulk material handling operations from closures, caps and preforms to liquids and produce.
PLASTIC IBC’S WITH LINERS – AN EFFECTIVE SOLUTION FOR LIQUID HANDLING
Innovative, foldable plastic IBC’s effectively handle liquids with the use of a liner bag, as supplied by Schematic Engineering Industries.
The hygienic liner bag is inserted into the foldable IBC and the liner is filled before being sealed at the supplier premises.
There are many valve inlet position options and liner material options which cater for ALL industrial/client applications.
Once filled, the triple-skin IBC liners are effectively protected by the walls of the plastic IBC during storage and transport. This includes the use of a sump cover to protect the liner discharge outlet valve, positioned at the base of the plastic IBC.
PLASTIC IBC’S – THE 10 SIMPLE STEPS TO USE THE LINER
Plastic IBC Liners are used extensively by many thousands of global clients. The 10 simple steps to use the Schematic plastic IBC and liner are shown below.
STEP 1 –Place the Liner at the base of the plastic IBC and open it out. The IBC dropdown doors facilitate easy operator reach to the base of the IBC.
STEP 2 –Align the green discharge valve with IBC sump cover orifice.
STEP 3 – Insert the U-shaped push clip (black) into the discharge valve to clamp it in place.
STEP 4 – Upwardly rotate the green discharge valve and insert it into the IBC sump orifice. It will automatically and securely click into place.
STEP 5 – Remove the blue plastic sealing cap from the filling orifice of the liner.
Note: The smooth walls of the Schematic plastic IBC effectively support the liner during filling.
STEP 6 – Connect the stainless steel filling adapter to the liner and connect the filling hose.
STEP 7 – Fill the liner with the liquid. The liner automatically expands/unfolds as the liquid is filled.
The plastic IBC walls provide consistent thermal heat transfer and therefore effectively eliminate the produce/liquid quality discrepancies associated with metal framed IBC’s, described previously.
STEP 8 – Detach the filling hose and then detach the stainless steel filling adapter.
STEP 9 – Re-attach the blue liner sealing cap back on the liner filling orifice.
STEP 10 –Fit the black IBC lid on the plastic IBC. The lid will automatically and securely click in place. Then connect the anti-tamper TE Pins on the lid and sump cover.
The liquid filling operation is now complete, and the plastic IBC can be stored (and stacked up to 5-high) awaiting transportation to the process plant/client.
SUMMARY – INNOVATIVE PLASTIC IBC’S ARE THE SOLUTION FOR LIQUID HANDLING AND TRANSPORT
The experienced reader will understand the huge benefits of the Schematic foldable plastic IBC’s with liners not only for the processing plants/clients requiring liquid produce, but also for its supply chain. Such benefits include:
· Return Transport fuel/emissions savings.
· Warehouse storage space savings.
· Stackable – The Schematic IBC;s can be stacked up to 5 high at full contents capacity.
· Improved Health and Safety for plant and operators.
· Reusable - Typically the plastic IBC’s have an operational life of up to 10 years without issue.
· Easy to clean. The smooth side walls of the IBC are crevice free.
· The liner is a consumable item which can be disposed of or sent for recycling after use.
· The annual cost savings of the consumable liners compared to HDPE blow moulded containers is huge.
To download the full technical paper of this article, please click here