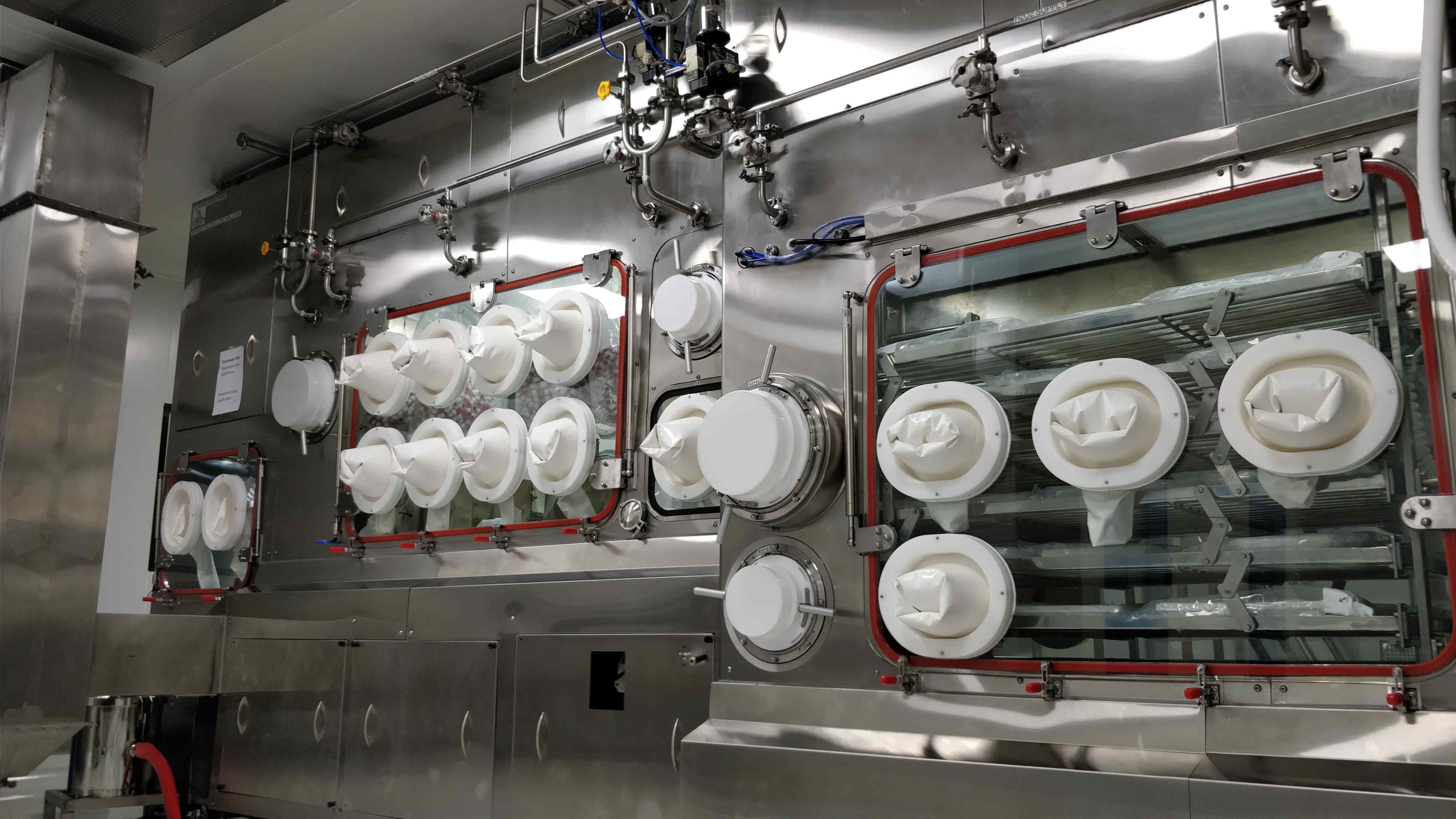
Navigating the dynamic landscape of pharmaceutical manufacturing demands an unwavering commitment to safety and quality. In this highly regulated environment, the strategic implementation of isolators emerges as a crucial element in achieving these non-negotiable objectives. In this article, we will delve into the significance of isolators by exploring their definition, the various types available, and the pivotal role they play in the intricate processes of pharmaceutical manufacturing. Additionally, we will introduce our wide range of products and services designed to enhance and streamline your pharmaceutical manufacturing processes.
An isolator is a highly advanced containment system designed to provide an isolated environment for the handling of sensitive substances, such as potent pharmaceutical compounds or hazardous chemicals. This innovative technology serves as a protective barrier between the operator and the materials being processed, minimising the risk of contamination and exposure, thereby ensuring a sterile and controlled atmosphere within the isolator.
Barrier isolators are advanced containment systems designed to create a protective barrier between the operator and sensitive materials. They are particularly crucial in handling potent pharmaceutical compounds or hazardous chemicals. The primary purpose is to minimise the risk of contamination and exposure, ensuring a sterile and controlled atmosphere within the isolator.
Applications of Barrier Isolators:
Aseptic isolators are specifically designed for aseptic processing, demanding a sterile environment to prevent microbial contamination. They play a crucial role in the manufacturing of sterile pharmaceutical products, ensuring the integrity of the final product.
1. Contamination Control: Isolators are paramount in maintaining stringent contamination control, serving as robust barriers against microbial and particle contamination to ensure the purity of pharmaceutical products.
2. Operator Safety: The physical separation provided by isolators acts as a protective shield for operators, mitigating the risk of exposure to hazardous materials, contributing to a safer working environment.
3. Product Quality Assurance: Isolators establish controlled environments crucial for product quality assurance. They prevent variations in composition, ensuring consistency and reliability in pharmaceutical products.
Schematic Engineering Industries offers a comprehensive range of isolators, including glovebox isolators, containment isolators, aseptic isolators, API isolators, formulation isolators, and injectable isolators. Our products are meticulously crafted and rigorously tested to meet and exceed industry standards, catering to the diverse needs of pharmaceutical companies worldwide.
Explore our products here.
For more information about our cutting-edge products and services and how we can assist in optimising your pharmaceutical manufacturing processes, contact us today. Our commitment to safety, quality, and innovation makes us a trusted partner in the dynamic landscape of pharmaceutical manufacturing.