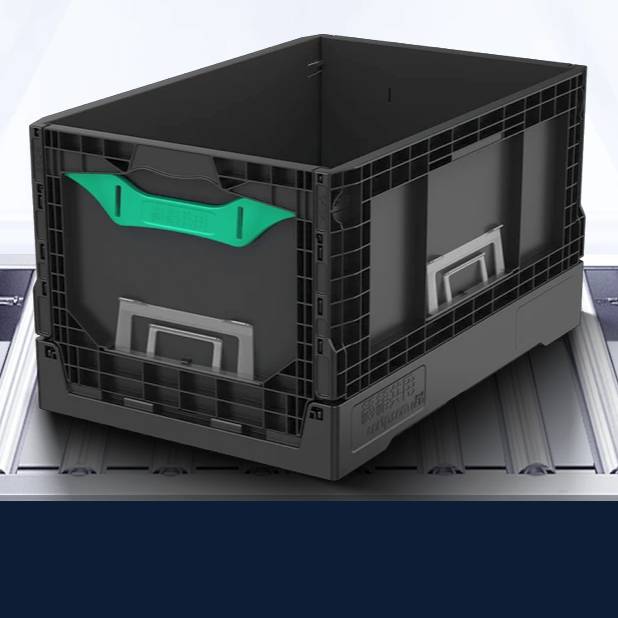
FOREWORD: “Design is a Compromise”. That is a given fact. Often, designers must make certain design decisions depending on many factors, not least target manufacturing price, the manufacturing tooling/machines available to make the product, avoidance of patent infringement and material selection/availability. These “design laws” are applicable across all products, from cars to crates. Crates are a necessity of today’s world and folding crates have huge client benefits, however not all folding crate designs are the same. There are good designs and ‘not so good’ designs.
DISCUSSION: The packaging sector supplies products across all industry sectors from food to pharma. Containers and crates are essential for warehousing operations and for transporting goods from company to company.
Crate and Intermediate Bulk Container (IBC) innovation has taken off in the last few years. Folding IBC and crate designs are increasingly being adopted as clients build huge warehouses to move crates and IBC’s around their facilities integrating them with conveying equipment, tipping and dispensing equipment alike.
This paper explores some of the crate design features encountered on the market and which should be avoided where possible.
From Figures1 to 5, the reader will note that there are many folding crate designs on the marketplace today, each with different design features.
Some have solid side panels. Some have vented side panels. It stands to reason that if the weight of the crate is important, a vented side panel design will be lighter than a solid side panel design.
However, the vented holes/slots create a weak area of the crate, as the material is thinner around these hole/slot features. It stands to reason that vented crates are more likely to crack and split and fail compared to sold side panel designs because of this design feature.
Let’s breakdown the critical features of a folding crate further:
The critical feature on any folding crate design is the HINGE design.
It stands to reason, that during the folding and un-folding operation, the hinge will be subject to movement and potentially operator mishandling.
Therefore, a robust, strong hinge design is essential.
[1] MATERIAL AROUND THE HINGE SIDEPANEL - ISSUE 1
From Figure4, the crate shown does not have “material webbing” around the hinge area of the side panel, as shown below.
In comparison, the design shown in Figure 1 as webbing around the entire crate circumference side panel(s). An extract is shown below.
The experienced reader will understand that the webbing provides considerable strength to thin plastic sheets. This strength is ESSENTIAL around the hinge area of a folding crate as it helps to prevent the operational stresses of the fold/un-fold being transmitted to the thin plastic sheet (crate side panel/wall).
FACT -Crates will fail if the material around the hinge area is not designed well. Providing strength to the thin plastic side panel connected to the hinge is essential.
Although, arguably more expensive to manufacture (as more material is used), a crate with webbing around the full hinge circumference is an excellent mechanism to provide side panel strength and thus hinge longevity.
[2] MATERIAL AROUND THE HINGE JOINT -ISSUE 2
The material around the hinge joint itself is also critical.
By way of example only, from Figure 4, the crate design has unequal amounts of material on the corresponding panels that make up the hinge joint. This is enlarged in the image to the right, depicted by sizes “A” and “B”.
This design typically means that the hinge element in one panel (with more material) is likely to be stronger than the hinge element in the corresponding other panel (with the smaller material).
The point being, like the links of a chain, the crate hinge design and strength is ONLY AS GOOD AS THE WEAKNESS point.
If one part of the hinge is weaker than another part, the hinge will most likely fail at the weaker part, irrespective of how strong the other part of the hinge is.
By comparison, an extract of Figure 1 shows the hinge in this design has relatively equal amounts of material on each element that make up the hinge. This is shown in the extract image below.
It stands to reason that a design with EQUAL amounts of material on both elements of a hinged crate design, both parts of the hinge will be EQUALLY as strong. Hinge failure is therefore less likely with this design.
SUMMARY – DESIGN IS A COMPROMISE
We would all hope that product designers do not make bad designs on purpose. Every design feature is a compromise.
Sometimes the compromise comes down to the experience of the designer and his/her technical knowhow and real-world awareness of the product in service.
Sometimes the compromise comes down to the target selling/manufacturing price that the manufacturing company is aiming for.
Sometimes, in the case of moulded plastic crates, the compromise comes down to the mould tool design and its complexity.
Whatever the compromise, understanding the potential failure modes in ANY product and mitigating these by selecting a superior, stronger, better made quality product, is always a good choice for a client who works in a business that is operational quality and reliability focused.
To download the full technical paper of this article, please click here