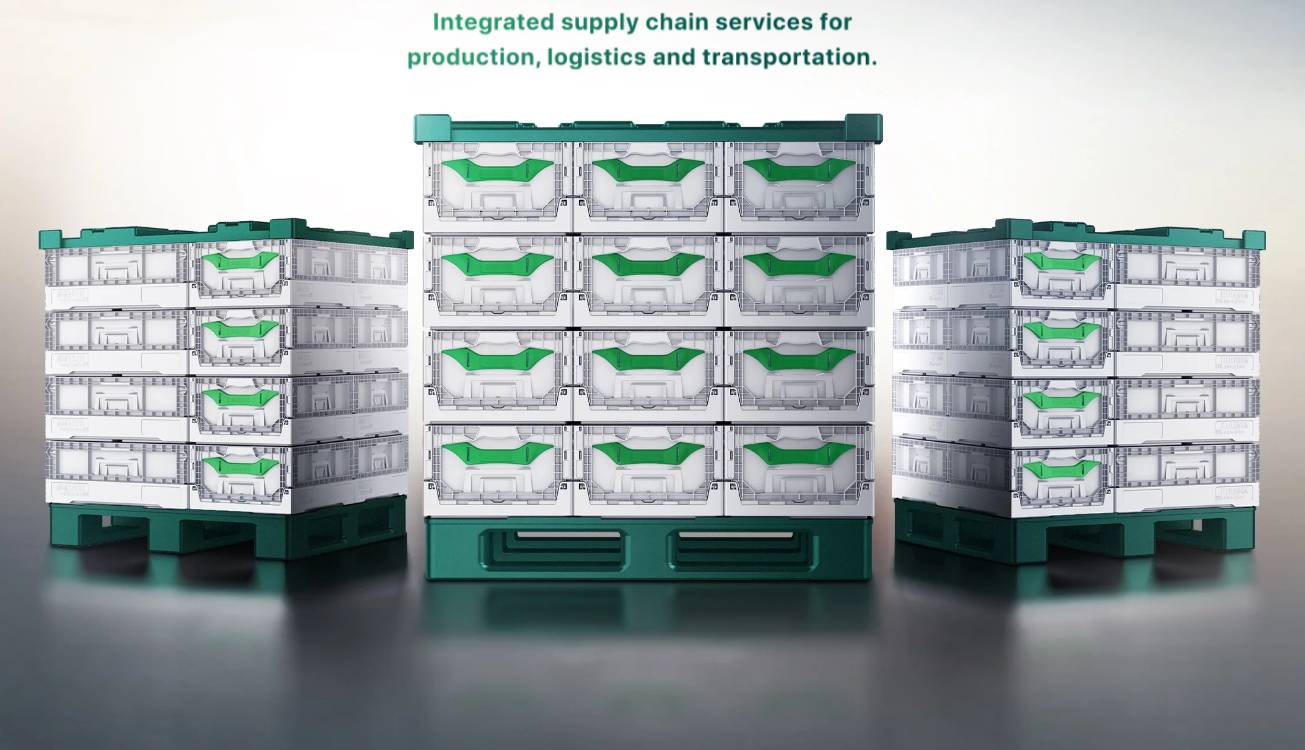
FOREWORD: Product design integrity is key to sustainable performance and crate/container operational longevity. Reputable companies evaluate and develop products in accordance with best practice techniques, innovative ideas and in conformance to international testing standards.
International testing standards for crates include:
- General simulation performance test for packaging (ISTA-3E)
- D4169 -08 Performance Testing of Shipping Containers and Systems by the International Safe Transit Association (ISTA)
- American Society for Testing and Materials (ASTM)
Clients selecting a container/crate supplier should always review and understand the supplier’s product testing certification and testing investment/facilities that verifies that the crate/container is fit-for-purpose.
DISCUSSION: Crate failure can occur due to various factors, including inadequate design, material weakness, improper construction, or extreme conditions during transportation or storage. Here are some common crate failure modes:
[a] Structural Failure: This occurs when the crate's structural integrity is compromised, leading to deformation, collapse, or breakage. Structural failure can be a result of insufficient load-bearing capacity, weak joints or fasteners, or inadequate material strength. In the case of a folding crate/container, the design, strength and durability around the folding hinge is key.
[b] Impact Damage: If the crate is unable to protect the contents from impacts during handling or transportation, it can result in damage to the product inside. Impact damage can occur due to insufficient cushioning or shock absorption, poor crate design, or inadequate protection against external forces. Plastic crates which are particularly STIFF and RIGID are less likely to provide shock absorption and more likely to crack/be damaged.
[c] Compression Failure: When the crate is subjected to vertical pressure from stacking other crates or heavy loads, it may experience compression failure. This can result in the collapse or deformation of the crate, potentially leading to damage or breakage of the contents.
[d] Moisture or Water Damage: If the crate is not adequately sealed or protected against moisture, it can result in water infiltration. Water damage can weaken the crate's structure, cause material deterioration, or result in mould or mildew growth, potentially damaging the contents. This is only relevant if the crate is used outside, and not in an internal warehouse environment.
[e] Environmental Degradation: Exposure to extreme temperature variations, UV radiation, or other environmental factors can degrade the crate materials overtime. This can lead to brittleness, weakening, or degradation of the crate, reducing its protective capabilities.
[f] Inadequate Load Distribution: If the contents of the crate are not properly distributed or secured, it can lead to shifting or movement during transportation. Improper load distribution can cause excessive stress on certain areas of the crate, leading to localized failure or increased vulnerability to damage.
[g]Insufficient Cushioning: If the crate does not provide adequate cushioning or shock absorption, it can fail to protect the contents from impacts, vibrations, or other external forces. Insufficient cushioning can result in product damage due to excessive movement or contact within the crate.
To mitigate these failure modes, crate design and construction should consider factors such as load capacity, material strength, cushioning, secure fastening mechanisms, and protection against environmental factors. Regular testing and evaluation of crates under realistic conditions can help identify and address any potential weaknesses or failure modes.
INTERNATIONAL STANDARDS FOR TESTING OFCRATES
Reputable manufacturers therefore verify that a crate design is suitable for its intended application through a series of tests and simulations to evaluate its performance, durability, and safety while being transported or stored in a crate or packaging.
Crate testing is commonly conducted to ensure that the product and its packaging can withstand the rigors of transportation, handling, and storage without damage. Typical testing include:
1.0 Drop Test:
The crate is dropped from a specified height onto a hard surface to assess its ability to protect the contents from impact forces. International testing best practice states crates to be ‘Free-fall drop tested, with Full load from 1.2m high. This should be repeated at least 3 times.
2.0 Vibration Test:
The crate is subjected to vibrations simulating various transportation conditions, such as road or air transport, to evaluate its resistance to vibration-induced damage. International testing best practice states crates stacked on two pallet stacking are set root mean square acceleration Grms=0.54 and perform a 4-hourrandom vibration test at 1-200Hz.
3.0 Compression Test:
The crate is subjected to vertical pressure to determine its ability to withstand stacking loads and prevent the contents from being crushed. International testing best practice states crates are to be placed in the centre of the pressure platform, and pressurize F=Wts(S-1)xFxJ for 1 hour, where Wt is the total weight of a single full-load crate, S is the number of layers, F is the safety factor=3, and J is the gravity constant=9.8N/kg.
4.0 Impact Test:
The crate is subjected to an impact force on all four sides, to assess its resistance to sliding and impact forces during transport. International testing best practice states crates are to be Two-pallet stacked and impact the 4 sides at a final velocity of 1.1m/s.
5.0 Environmental Test:
The crate is exposed to various environmental conditions, such as rain, dust, or sunlight, to assess its ability to protect the contents from such elements. International testing best practice states crates are Free-fall dropped at low temperature under a no-load crate condition at -20°C for 48 hours, and drop it from the height of 1m; for each time the sample passes the test, the height is increased by 0.3m.
6.0 Stacking Test:
The crate is stacked with other crates to evaluate its strength and stability under stacked conditions. International testing best practice states single crates, with no load are placed between plates, the upper pressure plate of the pressure tester pressurizes at a speed of 13mm/min until the sample is crushed.
Crate testing helps manufacturers and logistics providers ensure that their products are adequately protected during transportation and storage. It also helps identify any weaknesses or design flaws in the packaging, allowing for necessary improvements to be made. Most of all, it provides client assurance that the product they are looking to purchase/invest in for their operations, is fit-for-purpose.
TESTING OF SCHEMATIC “EUO” CRATES
The EUO range of crates, supplied by Schematic, have been tested in their in-house world class test facilities (shown below) in accordance with the pre-mentioned international testing standards. This is summarised below. This helps to ensure that the Schematic EUO crates are best in class and fit-for-purpose.
Figure 1 – The World Class Test facilities of the Schematic supplied Crates
Figure 2 - Testing summary of the EUO crate, supplied by Schematic Engineering Industries
SUMMARY – DESIGN VERIFICATION THROUGH COMPREHENSIVETESTING IS ESSENTIAL
Reputable companies develop and supply products which are verified through comprehensive product verification testing to international standards.
Crate weight is optimised and minimised wherever possible to reduce operator ergonomic strain and injury when repeated lifting and manual handling. At the same time, product strength and durability is maximised through Finite Element Analysis (FEA) and design optimisation to ensure product longevity.
After manufacturing, best practice companies push their crates/containers through a comprehensive product testing regime that simulates advanced real-world situations.
Clients should therefore align themselves with suppliers who can demonstrate investment and competence in crate and container design and testing.
To download the full technical paper of this article, please click here